Enhanced Wastewater Management at Nestlé Smithtown: Reducing Phosphorus Accumulation with Advanced Dewatering Technology
Nestlé’s Smithtown factory, a key facility in Australia known for producing powdered beverages such as Milo, Nesquik, and Nescafé coffee mixes, has recently upgraded its wastewater treatment process to address a significant operational challenge. The factory’s existing wastewater treatment plant (WWTP) was based on an intermittent activated sludge system, specifically a Sequencing Batch Reactor (SBR). The Waste Activated Sludge (WAS) produced by the SBR was historically diverted to an anaerobic digester, with the excess water from this process being returned to the SBR.
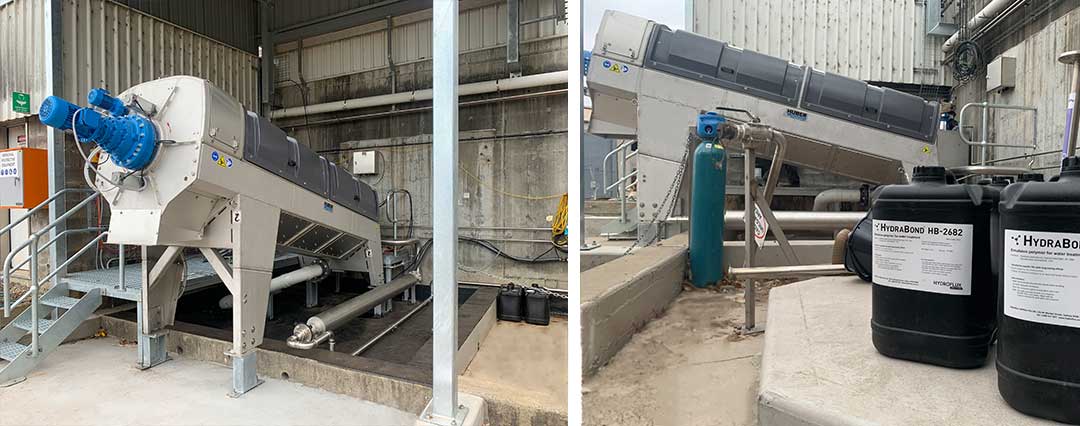
However, one of the consequences of this anaerobic digestion process is that the phosphate stored within the biomass during the digestion process was released back into the liquid phase when the excess water was returned to the SBR. This resulted in a gradual buildup of phosphorus in the system, which could impact the efficiency of the wastewater treatment process and the quality of the treated water.
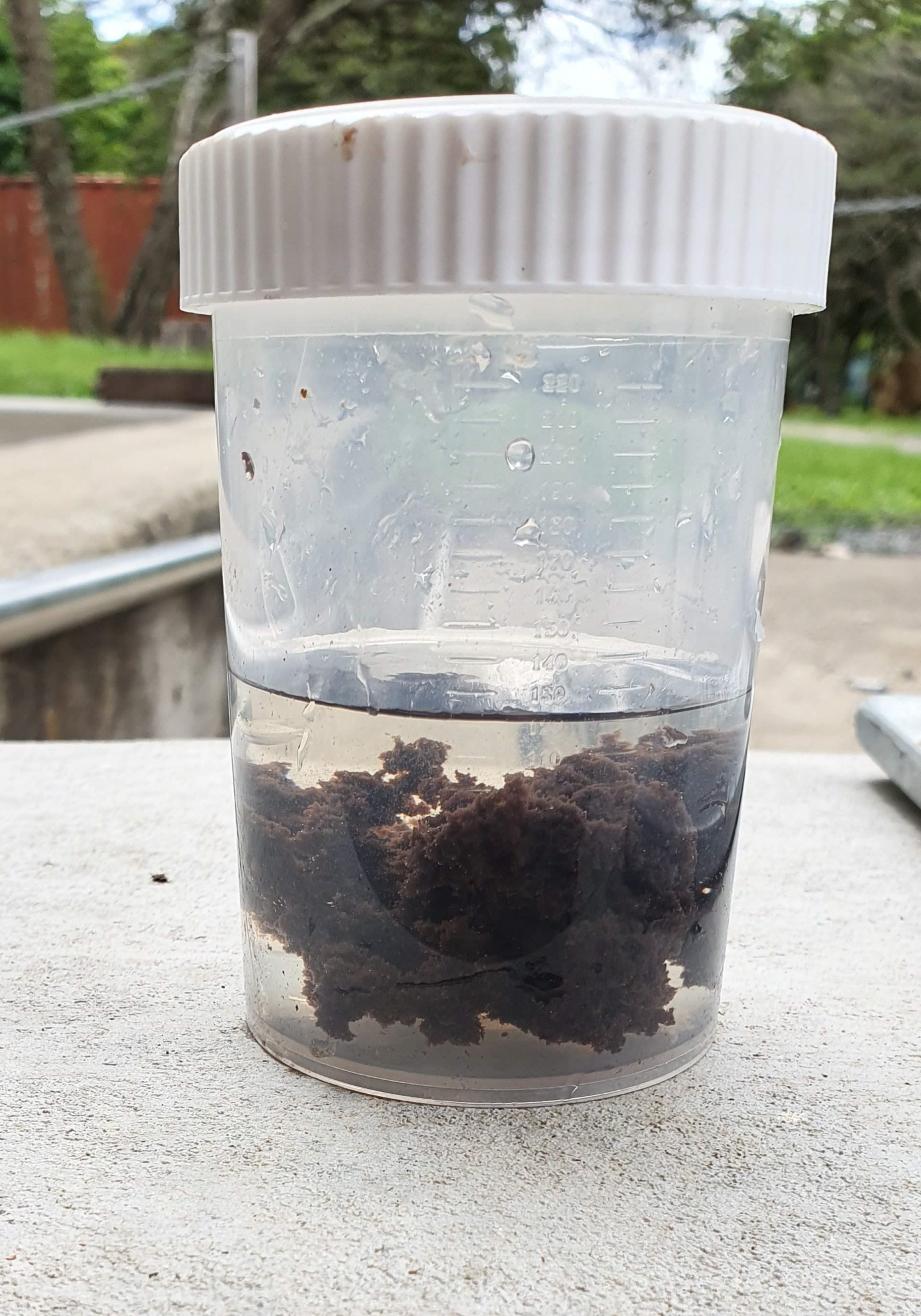
To address this issue, Hydroflux was engaged to implement a new WAS dewatering system that would replace the anaerobic sludge digestion process, thereby preventing the release of phosphate back into the SBR. The solution involved the installation of a HUBER Q620 dewatering unit which is capable of effectively dewatering very low concentrated solids directly from the SBR during aeration cycles, when the solids feed is constant.
The HUBER Q620 unit, with a capacity of up to 10 kL/hr and a solids load handling capability of up to 350 kg/hr, was selected for its efficiency and reliability in such applications. By retaining phosphate within the solid waste, this system significantly reduces the concentration of phosphate returning to the SBR, thereby preventing the accumulation of phosphorus and enhancing the overall effectiveness of the wastewater treatment process.
This turnkey project included the supply and installation of the screw press and the HydraBLEND polymer system but also included all necessary civil, mechanical, and electrical works. This involved intricate tie-ins to the existing infrastructure and Building Management System (BMS), to retain the WWTP online during construction.