Hygienic HyPURE® System for Food and Beverage Production
Hydroflux have completed commissioning of a new 2.4 MLD water treatment plant for an iconic Australian soft drinks manufacturer in Queensland. The project was awarded to Hydroflux in 2020 as part of the construction of a new $150 million production facility.
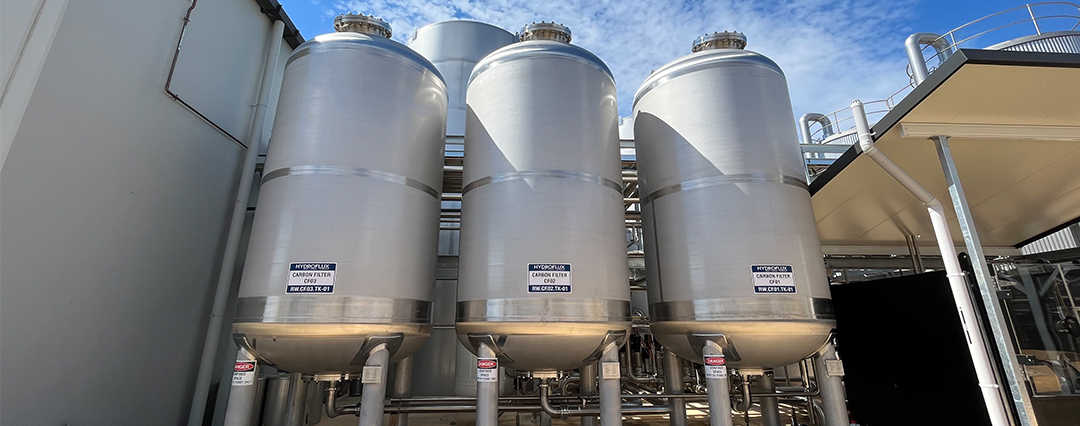
The project consisted of two HyPURE® filtration processes. The first is a hygienic activated carbon system for the removal of free and combined chlorinated compounds from town water. Hydroflux were engaged to design and supply 3 x 50m3/hr SS316 hygienic activated carbon filtration vessels. The vessels were designed for contact with final product water and included the capability for routine in-situ steam regeneration to maintain the hygienic environment throughout the service life of the system.
Through the process of reduction, the activated carbon converts the free chlorine within the town water to chloride ions, whilst adsorbing disinfection byproducts onto the media bed. Periodic backwashing of the vessels removes fine suspended material, organics and bacteria.
The routine steam regeneration recovers the carbon media by stripping organics and simultaneously sterilising the bed.
Sustainable utilisation of water resources was a key driver for the new facility. Our client was driven to minimise the demand on the local potable water supply. To maximise the water efficiency of the site, the second package supplied by Hydroflux included a HyPURE® ultrafiltration system to recover 300 m3/D of activated carbon backwash water and bottle rinse water for reuse.
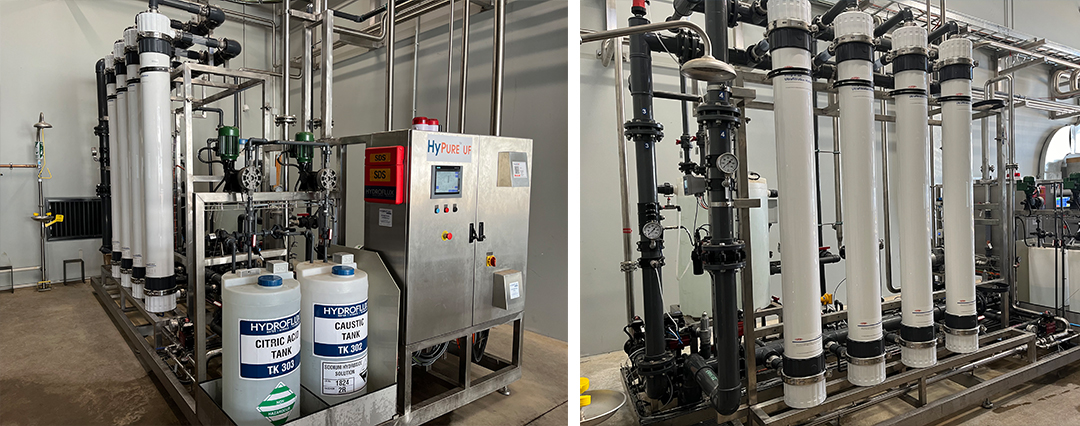
Due to the limited data available to design the system, the client’s engineer and Hydroflux worked together to develop the project. Through our extensive experience in the development and execution of backwash recovery projects, Hydroflux were able to identify the potential risks and present a robust design to meet the client’s performance expectations.
One of the key challenges to the project was the variable feed water quality across the backwash and bottle rinse water. A conservative flux design was implemented to ensure the process is capable of handling the variability. Spare racking space was made available for additional membranes if required in future.
The system also features an advanced PLC and HMI control system, a fully automatic cleaning system with heater to maximise the life of the hollow fiber membranes and the HyCONNECT™ remote monitoring system to provide on call client support when required.
The HyPURE® systems were successfully commissioned at the end of 2023. The HyPURE® activated carbon filtration vessels are producing water which is now forming part of the final beverage products to be shipped around the world. The HyPURE® ultrafiltration system is exceeding the original design recovery performance.